In today’s competitive environment, the efficiency of fleet operations plays a pivotal role in achieving higher productivity and healthier bottom lines. The collaboration between Summit Truck Bodies and Miller Electric Mfg. LLC., demonstrates a collaborative synergy—leading the charge in offering fleets more streamlined and effective solutions.
The result? A powerful combination that lets fleets accomplish an unprecedented level of work, while reducing their environmental footprint.
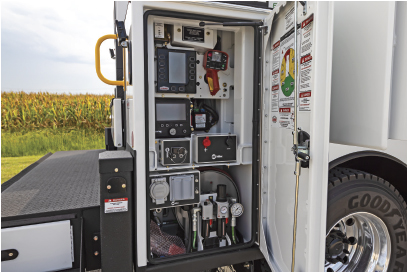
BORN FROM NECESSITY
At the heart of this collaboration lies a shared vision between Summit and Miller: Summit is in the business of crafting world-class truck bodies, tailoring them to specific client needs; Miller Electric is renowned for its stellar welding solutions and integrated truck systems. As fuel costs surge and emission regulations tighten, customers yearn for a solution that will let them harness the full potential of their service trucks without running their diesel engines. The Miller EnPak power system mounted on a Summit work truck is a game-changing combination that addresses these needs.
Both companies concede that the whole value of integrating a Miller EnPak with a Summit body is worth far more than the sum of its parts. Both organizations share a commitment to quality, highlighting the opportunity to deliver greater value to end users that this collaboration represents.
ENPAK IN ACTION
The engine in a work truck is designed to move that truck and everything in it, hauling thousands of pounds over thousands of miles with the best balance of power and efficiency. Today’s emission-compliant truck engines are not designed to power welders, jobsite tools, pumps, and accessories as efficiently as the EnPak power systems.
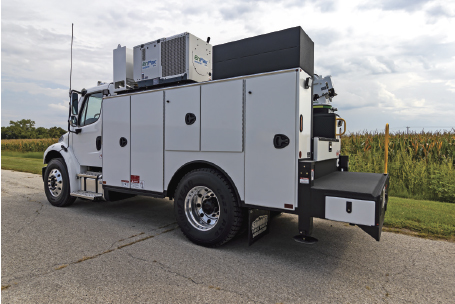
Miller’s variety of EnPak power systems are productivity-boosting combinations of an air compressor, generator, and available hydraulic pump that are powered by a fuel-efficient diesel engine, all of which are integrated with the truck’s fuel supply and battery. EnPak systems provide users with full jobsite functionality—even with the work truck’s engine turned off.
Using an EnPak system instead of the engine of a diesel work truck can greatly reduce the expense of servicing that truck’s emission-control equipment. EnPak systems are powered by a 24.8-horsepower diesel engine that meets all applicable Tier 4 Final (T4F) regulations mandated by the EPA, producing fewer exhaust emissions and improved output for a wide variety of job requirements.
“We tested the Miller EnPak concept back in 2012. After closely following two of our service trucks outfitted with EnPaks and two traditionally built with PTO drives, we realized a 16% reduction in fuel consumption alone,” says Patrick Overstreet, director of Product Support for Ascendum Machinery. “Over the past 11 years, we have seen a cost reduction in emission repairs and engine idle hour-related repairs.”
COMPLEMENTARY FORCES
The logic of the collaboration between Summit and Miller is evident in how seamlessly their products come together. Summit’s custom truck bodies are meticulously designed to work in tandem with multifunction units like the EnPak. One standout feature is the crane remote controls.
“Our crane remote controls, which usually communicate with the chassis, are now designated to interface with the Miller EnPak unit,” says Brent Thompson, product development specialist for Summit. “This allows for smooth operation of engine start, stop, and speed control functions as if communicating with a chassis.”
The benefits? Reduced chassis run time, minimized service and repair costs, and the provision of a crane function akin to a chassis PTO-mounted hydraulic pump. Thompson compliments the resilience of the integrated Miller system, saying, “Like our truck bodies, the EnPak is designed to not only survive, but thrive in extreme environments.”
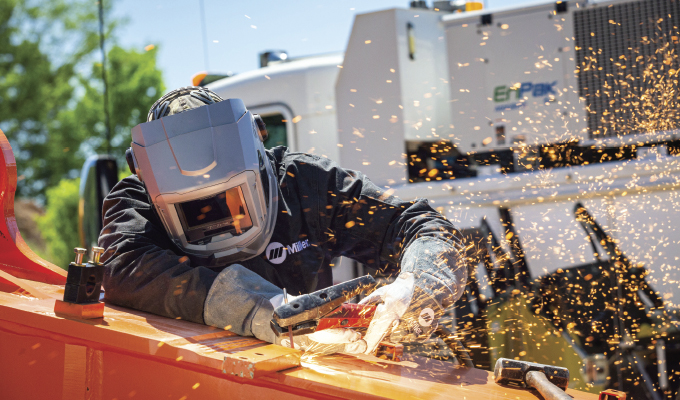
PRODUCTIVITY GAINS
When asked about the tangible benefits of this solution, both companies are unanimous about the efficiency and cost savings. Both highlight the EnPak’s role in reducing chassis run time and minimizing service and repair costs.
“Fleets can expect that when their Summit truck, with an integrated EnPak system, pulls up to a jobsite, their technicians can get the job done,” says Max Charlton, territory manager-west of Work Truck Solutions / Power Systems Division at Miller. “Whatever work needs to be executed in the field can be completed in a timely manner—meaning more work—resulting in more revenue.”
METICULOUS INTEGRATION
System integration is simply based on the end user’s specifications and Summit’s ability to match those specifications. An EnPak can be mounted almost anywhere on the truck bed, while other components like user interfaces, weld panels, and auxiliary power panels can also be mounted at custom locations. The EnPak only needs to be wired to the chassis’ battery and connected to its fuel supply as well as its hydraulics and crane, if applicable.
“One of the challenges we face is balancing the ideal mounting location with the preferred aesthetic location of the EnPak. To achieve this, our design team collaborates closely with customers, drafters, and sales professionals to ensure immediate functionality, long-term reliability, and customer satisfaction,” emphasizes Thompson. “Customers invest a significant amount of money in our truck bodies and value not only their functionality, but their overall appearance as well.”
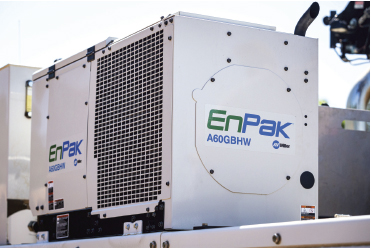
FEEDBACK & ADAPTATION
One hallmark of a successful collaboration is the ability to evolve based on feedback and real-world demands. Miller’s approach to their EnPak system is a testament to this adaptability. The first-generation EnPak A60 didn’t include a welding feature, so users needed to rely on external plug-in welders. However, based on customer feedback, Miller introduced a 325-amp multi-process welding feature that’s fully integrated into the newer EnPak versions. They listened, adapted, and improved.
Charlton explains that another challenge addressed was the degradation of engine power at higher altitudes. He says, “To address this, a turbo was added to the diesel engine in the EnPak.”
Furthermore, recognizing the diverse needs of different operations, Miller unveiled an A60 version that boasts a generator, battery boost/crank assist, and the multi-process welder, sans the hydraulic pump. Charlton adds, “This kind of responsiveness underscores Miller’s commitment to maximizing field productivity.”
BEYOND JUST POWER
Miller’s EnPak system isn’t just about power—it’s about intelligent power. The EnPak’s tie-in with the chassis battery is revolutionary. For technicians out in the field, this means, even when they have lights on or equipment charging, the EnPak can autonomously turn on to charge the chassis battery and ensure no unexpected shutdowns occur.
Moreover, the system’s Auto-Speed technology and Auto start/stop features facilitate adaptability to varied jobsite demands. Whether it’s operating a heavy-duty impact tool, lifting with a crane, or conducting weld repairs, the EnPak A60 system’s features, such as the air compressor power, generator power, battery charge, hydraulic power, and integrated welding, ensure it can handle it all—often and simultaneously.
FUTURE-READY COLLABORATION
The synergy between Summit Truck Bodies and Miller Electric Mfg. LLC. is not just about two companies coming together: it’s about a shared vision of future-ready solutions for fleet operations. As regulations tighten and the operational landscape becomes more challenging, partnerships like this will pave the way for smarter, more efficient, and more environmentally conscious fleet solutions.
“Our build standard for Summit service trucks requires the Miller EnPak, and that has been our standard for over 8 years now,” says Overstreet. “We have been very pleased by the trucks and units, their reliability, and the incredible support that has followed them both after the purchase,”
“In the end, it’s about enabling professionals to do their jobs more efficiently, ensuring they can return to their families after a hard day’s work, and having accomplished more than ever before,” comments Thompson. “With Summit’s world-class truck bodies and Miller’s pioneering EnPak system, fleets are not just equipped for today’s challenges, but are future-proofed for tomorrow’s opportunities.”
FOR MORE INFORMATION
To find out more, visit www.summitbodies.com and www.millerwelds.com.