Owners and users of bucket trucks and digger derricks are responsible for ensuring their equipment is inspected both a daily pre-shift and annually. While safety is the foremost concern, annual inspections can also reveal small operational issues before they cause serious, and possibly expensive, equipment repairs.
According to factory-trained technicians at Terex Service Centers, the following are some of the important inspection items. Most of them apply to either digger derricks or aerial devices, while the last two are specific to aerials.
INSPECT DECALS
Operational and safety decals provide valuable information to the users. Sometimes it’s not obvious what’s missing from the equipment if you don’t know what decals are supposed to be there. It’s especially important to make sure hand signal charts aren’t missing from digger derricks. Hand signals provide a means to communicate between the operator and ground personnel when they are in a noisy environment. Failure to communicate clearly could lead to possible injury or equipment damage and could result in an OSHA violation.
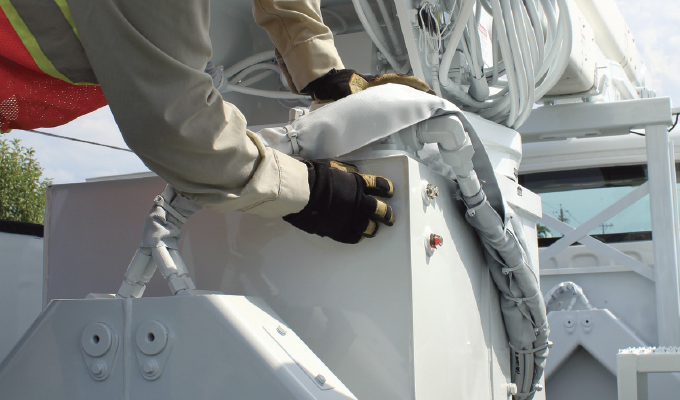
OIL & FILTERS
Oil levels must be checked according to the manufacturer’s recommendations for equipment to operate as designed. More frequent checks based on operating and weather conditions may be necessary.
Low levels, if left unattended, could lead to expensive, unplanned repairs. Burning up one pump can easily be a $2,000 repair, not to mention a loss in productivity from the equipment being out of service. Low oil levels are also an indication of a leak in the system that should be addressed immediately. High levels can also cause issues. Checking the fill level when the outriggers are extended can often lead to over filling, which leaves no room for expansion and can contribute to oil leakage.
A dirty oil filter can lead to accelerated wear and damage to pumps, cylinders, hydraulic valves, and hoses due to the fact the filter is no longer capturing harmful contaminants and particles circulating in the fluid.
WINCH ROPE
In addition to the daily visual inspection, the full length of the load line should be unspooled and inspected hand-over-hand during the annual inspection. Before inspecting, make sure to verify the type of rope used (for example, single braid, balanced double braid, or core-dependent double braid) and the appropriate inspection and replacement criteria for that type of rope. The best sources for information are the rope manufacturer or the Cordage Institute. The digger derrick ID plate will provide the minimum rope strength required of replacement ropes.
Among the conditions that should be reported to a qualified person to determine if the rope should remain in service are: excessive roughness, glossy areas indicating heat damage, flat areas or bumps/lumps indicating internal core damage, frayed strands, excessive wear, discoloration associated with chemical contamination, and stiffness due to embedded dirt or shock load damage. When you feel cuts, reduced section, or a bulge, it can indicate internal rope damage caused by shock loading or kinking, and the rope should be replaced.
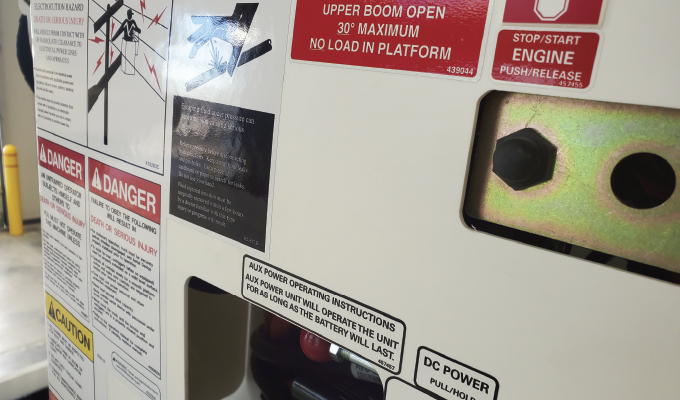
ROTATION BEARING BOLTS
While the process is simple, this is one of those items that cannot be overlooked. It may be easier to inspect and re-torque bolts with two people—one to rotate the bearing and the other to check the bolt torque. Information on the proper bolt torque and lubricant is available in the operator’s manual.
When using a socket with an extension, the torque value does not change. When an adapter, such as a “crow’s foot” is used, the torque value of the wrench must be adjusted to account for the change in distance between the center of the square drive and the center of the fastener being checked. Use information supplied with your torque wrench to make this calculation and adjustment.
Use the correct torque indicated in the manual. Do not jerk the torque wrench as you apply torque; instead apply even pressure. Find more information on how to check the torque on rotation bearing fasteners along with other inspection forms on the Terex website.
BEARING DEFLECTION
Checking the amount of allowable play in the rotation bearing takes time and a proper understanding of how to measure it. If there is too much play, this may be an indication that the rotation bearing could be worn and needs to be replaced. It could also be an indication that the boom has been shock-loaded and damaged the balls and raceway. Shock loading can occur any time a load suddenly drops and the boom stops the movement. An example would be a transformer slipping off its support and dropping until the load line stops it. Here’s how to measure it:
Attach the dial indicator base to the pedestal, positioning the tip perpendicular to the edge of the turntable bottom plate at the specified indicator radius shown in the unit specific manual.
Make sure you know which way the dial indicator rotates when it moves to get the correct reading.
Zero out the dial indicator. Verify that you have at least 0.25 inches of movement on the dial indicator in both directions when zeroing.
Position boom according to manufacturer instructions.
Read the number on the dial indicator. This is your rotation bearing deflection. Record the reading, and check this against “Maximum Allowable Bearing Deflection.” This value is based on a specific dimension of the reading from the centerline of rotation. This dimension is given with the maximum deflection.
LEVELING CHAIN
Leveling systems on aerial devices should have specific amounts of preload. Too much or too little tension increases wear and possible damage. Checking leveling tension requires taking off boom covers. Failure to keep the chain within tolerance could affect the self-leveling of the bucket as the boom moves through its range of motion.
Leveling chains should also be inspected for cracks, turned pins, or damage to the chain or links and should be lubricated with the proper lubricant, not grease, according to manufacturer recommendations.
CHAIN WEAR
One of the most important causes of premature wear or breakage is inadequate lubrication. In addition to reducing internal friction, maintaining a film of lubricant on all chain surfaces will inhibit rusting and corrosion. Under normal operating conditions, especially in dusty environments, lubricated chains will accumulate a paste-like buildup of grime. This buildup should never be permitted to accumulate sufficiently to seal off the clearances, thereby restricting the lubricant to the bearing areas. At periodic intervals, this buildup must be removed by cleaning and the chain immediately relubricated. Do not steam clean or use de-greasers; use a brush and a safe petroleum solvent such as diesel fuel or kerosene. Chains can also have specific inspections to measure wear or specific replacement intervals, see the manufacturer’s manual for the requirements. If unusual noise of jerking is reported inspect the tension and lubrication of the chains.
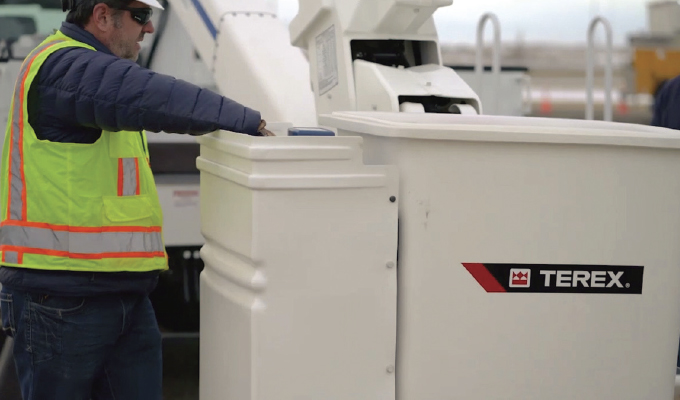
BUCKET & LINER
Cracks, gouges, and damage to the aerial device bucket could affect the structural integrity and contribute to reducing dielectric strength if the liner is damaged. Tools can get dropped, which damages the liner and the platform itself. It’s important to look underneath, inside, and outside the platform and liner by removing the liner. Liners also require periodic dielectric tests.
Annual inspections are a task to be performed by those qualified, such as Terex Utilities’ factory trained technicians who have access to the right tools to do the job correctly. For owners who perform annual inspections in-house, Terex offers several training programs on its website designed to provide technicians with the knowledge to become a qualified inspector.
ABOUT THE AUTHOR
Rob Morris is a regional operations manager with Terex Utilities. Terex Utilities is a leading global manufacturer of aerial devices and digger derricks for the electric utility industry and offers service and parts support across North America. Terex Utilities is a business group within the Terex Aerial Work Platforms Business Segment of Terex Corporation. Find out more, visit www.terex.com/utilities.