Inefficiencies in service workflows can increase equipment downtime in the shop. Fleet management solutions automate the service workflow and allow users to create, track, and communicate within digital work orders to improve productivity and quickly get assets out the door.
AUTOMATE DATA CAPTURE
When it comes to process and workflow improvements, data is a key factor in determining inefficiencies causing avoidable downtime. Knowing what to look for and which metrics to track can help work truck fleet managers quickly spot issues to address them early. While this can be difficult for fleets still tracking data manually, fleet solutions such as fleet management software (FMS) automatically collect, consolidate, and aggregate fleet data for you—including data from integrated solutions like GPS, telematics, fuel cards, and even third-party maintenance shops. Cleaner data provides better insights into service processes and compliance rates. Automated data collection helps fleets improve the quality and quantity of asset data and catch errors such as inaccurate odometer inputs and over-fueling. It also helps fleets understand inefficiencies in the service process.
Although asset breakdowns and repairs are the leading causes of unexpected downtime, that downtime can be further extended due to delays in the shop. In fact, shop delays can actually cause avoidable downtime even when it comes to scheduled maintenance. Understanding service duration versus time actively spent performing the service is the first step in managing avoidable downtime caused by service delays. Service duration is the amount of time an asset spends in the shop from drop-off to pickup. Tracking service duration and comparing it against active time technicians spend on a job helps surface process issues that could be costing your fleet time and money.
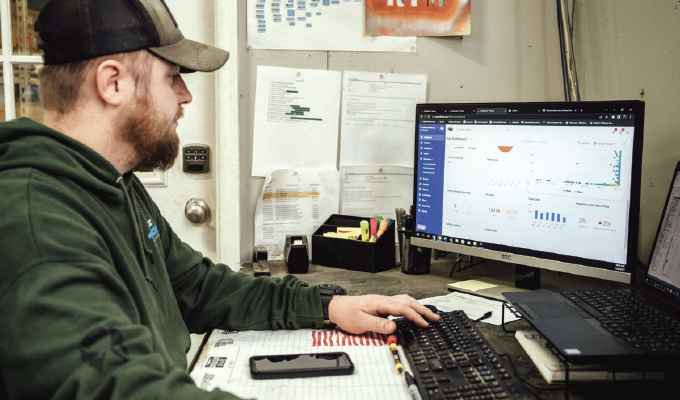
OPTIMIZE SERVICE WORKFLOWS
Surfacing the cause of service delays is critical to implementing a successful solution. Service delays can be caused by such issues as inefficient scheduling and/or staffing, poor communication, and delays in replacement parts acquisition. Fleets can use FMS to improve communication around service needs using service reminders. Service reminders help fleets stay on top of preventive maintenance and compliance, including receiving overdue and due soon service alerts. Fleet managers can set these reminders to be sent to anyone who needs to see them, such as account admins and managers, the driver to whom the asset is assigned, and the technician to whom the work is assigned. Using service reminders not only makes it easier to schedule service-related downtime, it also ensures everyone in the workflow knows when to be where, why, what’s being done, and when an asset is ready for pickup.
Fleets servicing trucks in house can also use digital work orders in FMS to track active service time, service duration, repair priority class (based on Vehicle Maintenance Reporting Standards), parts used, and all associated line item costs. Technicians can use the software’s native app to clock in and out of jobs for more precise service data and can communicate within the work order so all task-related communication is centralized, transparent, and easily accessible. Fleet managers can use customizable labels in digital work orders to further categorize the source of delays, including waiting on parts or waiting for an open technician.
Because service duration and active service times are automatically captured in the software in real time, fleet managers can quickly assess the amount of—and using labels, the reason for—service delays. Digital work orders also track work order statuses in real time (i.e. whether a work order is open, pending, completed, needs approval, or is approved). With this data, work truck fleet managers can implement a plan to optimize workflows and increase service efficiency to reduce avoidable downtime, whether that means improving parts inventory management, scheduling, or hiring additional technicians.
Fleet drivers can also use the software’s app to submit digital asset inspections in real time, and failed inspection items alert managers, kicking off the service workflow. This better allows drivers in the field to easily communicate asset health data and ensures the concerns they kick up are addressed. And since managers—and any other relevant parties—receive failed inspection alerts in real time, issues are less likely to compound into a breakdown event, reducing instances of unscheduled downtime.
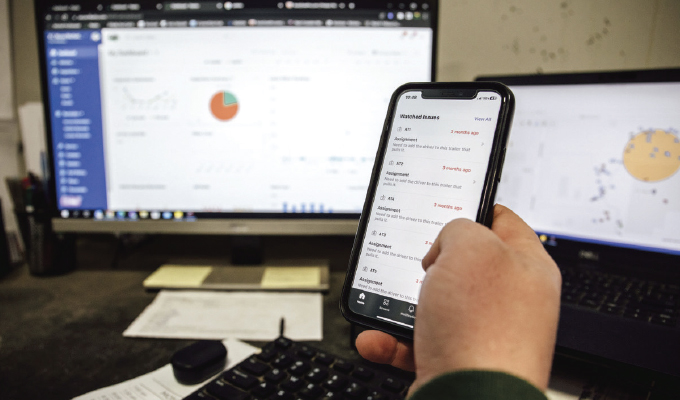
REAL-TIME REPORTING
Manually collecting service data isn’t just time consuming, it also increases the risk of data gaps, which can lead to inaccurate reporting, and it makes data consolidation and analysis more burdensome. Automated, configurable reporting is one of the top conveniences FMS provides. Plus, work truck fleets can use integrated FMS to automatically consolidate and aggregate data captured from other fleet solutions as well, reducing data overload.
Correcting workflow and process issues without knowing their source can prove to be quite a feat. Configurable reporting in FMS allows fleets to highlight key service metrics to monitor service workflow efficiency in real time and catch any problems as they arise. Furthermore, managers can tailor specific reports to stakeholders as needed, but this is especially helpful when it comes to advocating for needed resources to improve service workflows, including hiring more staff or making larger inventory purchase orders of high-fail parts to ensure your technicians have what they need to tackle the job.
Implementing FMS to track, monitor, and improve service workflows reduces avoidable downtime and ensures your assets are in safe operating condition for improved productivity and profitability.
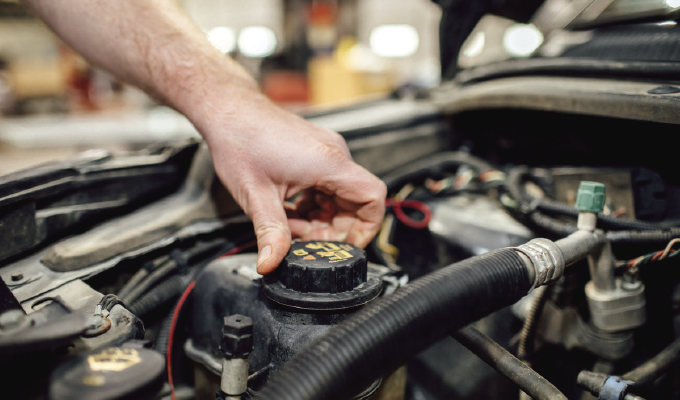
ABOUT THE AUTHOR
Rachael Plant is a content marketing specialist for Fleetio, a fleet management software company that helps organizations track, analyze, and improve their fleet operations. Find out more, visit www.fleetio.com.