In today’s vocational equipment environment, suspension geometry and spring type are the two biggest influences on driver comfort and equipment protection. Both factors should be considered along with service environment, duty cycles, and other critical details when specifying a suspension for a vocational truck. Nowhere are these considerations more important than in heavy-haul and severe-duty applications.
The two most basic categories of suspension geometry are: 1) Torque Reactive and 2) Non-Torque Reactive. Depending on the circumstances, both types of approach can provide any given vehicle with an adequate suspension, however, a Non-Torque Reactive suspension will provide the most comfort for a driver and the highest level of equipment protection.
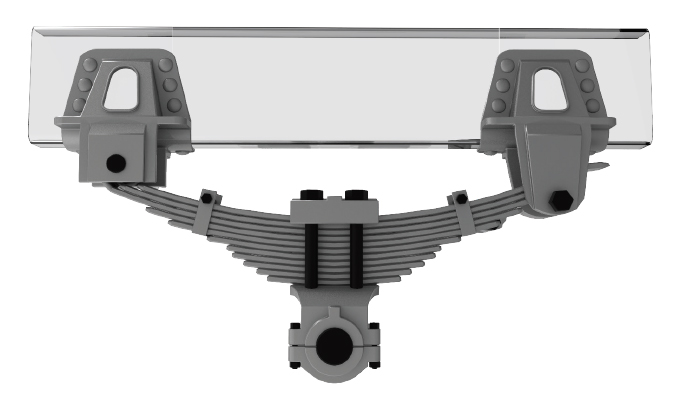
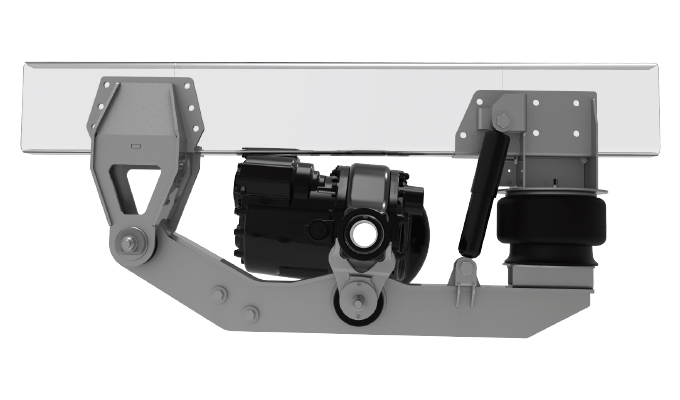
OVER REACTION
A torque reactive suspension will exhibit a vertical response during all braking and acceleration events. For example, if a vehicle is equipped with a torque reactive front suspension, the front of the vehicle will drop down when the brakes are applied. The more aggressive the braking event, the more pronounced the dropping experience will be for the driver.
If the vehicle has a torque reactive rear suspension, then the rear will drop down during braking as well, but it will also raise during opposing acceleration events. One can observe this when tractors or trucks are coming up to speed, because they will raise up and then drop down as the driver shifts gears. All this dropping and rising can not only cause wear and tear on all driveline components but will make the driver pitch forward and back in their seat. Even if the vehicle is outfitted with a high-tech seat that helps maintain driver stability, the vehicle’s steering wheel, gearshift, and the entire cab surrounding the driver can still be in dynamic motion.
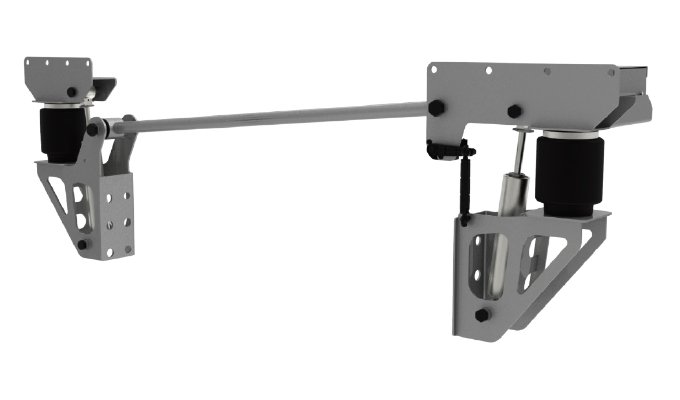
UPGRADE
If your application has a higher percentage of starts and stops and maneuvering, you should shy away from a torque reactive suspension geometry. If your budget will not allow you to upgrade to superior non-torque reactive suspensions, you may want to consider upgrading just the cab suspension.
Advanced cab suspensions like the Link ROI Cabmate, can help reduce the effects of torque reactive suspensions. Unlike traditional cab suspensions tuned to deliver a specific quality of ride only within a narrow range of surface and load conditions, the ROI Cabmate adapts to whatever it encounters.
The ROI Cabmate’s electronic control unit (ECU) uses proprietary algorithms to interpret a constant data stream from an accelerometer monitoring the motion of the cab and a position sensor measuring the position and velocity of the cab relative to the frame. The system responds at speeds beyond human perception, adjusting shock absorber stiffness with computer-controlled precision. The result is optimized ride comfort, improved cab stability, and an overall reduction in noise and vibration.
SPRINGING INTO ACTION
Spring type is the other big factor in a suspension’s ability to impact driver comfort. The three main spring types in order of least-to-best driver comfort level are: 1) Steel Springs, 2) Rubber Springs/Blocks, or 3) Air Springs.
The industry is trending toward using more rubber block walking beams and air spring suspensions. However, I believe the increase in using rubber block walking beams versus spring walking beams has more to do with weight reduction than comfort improvement. The unfortunate reality for drivers is that many rubber block walking beams almost go to a solid-mount state when fully loaded or in creep mode to protect rubber from being overstressed and breaking down.
The more interesting trend is with the acceptance of air ride suspensions in vocational applications. Air rides suspensions have been used in almost every vocational application going back more than three decades. However, as we are all aware, our industry moves cautiously, and because of a lack of familiarity, it may take many years for a fleet to become comfortable with ordering its next truck with air spring technology. At this juncture, I would estimate that 30 to 40% of the most severe-duty applications are now using air suspensions with the remainder using either spring or rubber walking beam suspension—with the higher share of those on rubber.
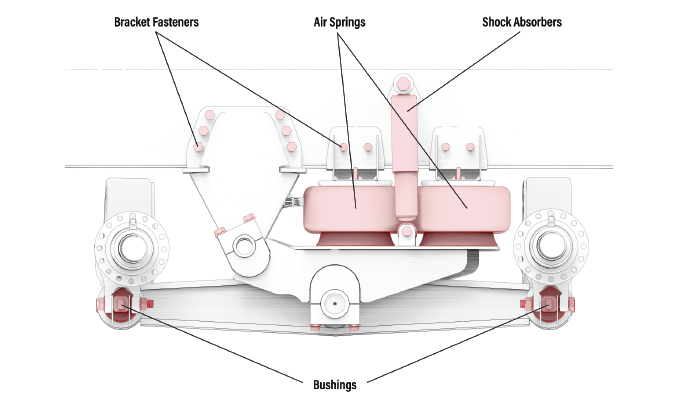
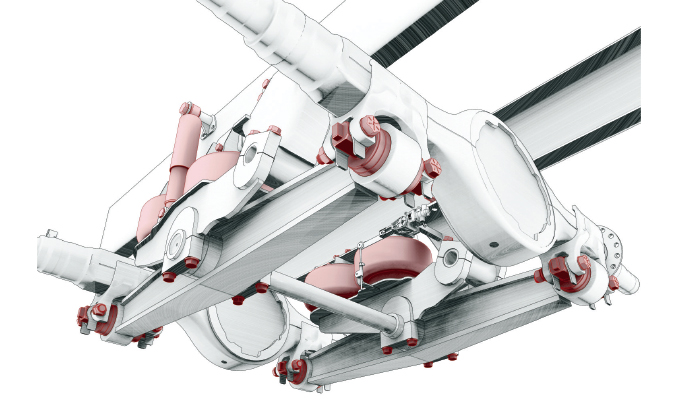
AIR LINK DIFFERENCE
Almost every truck runs empty for up to half of its life. This is especially true for vocational trucks such as dump trucks and cement mixers. Link’s air-over-walking-beam technology was patented close to 30 years ago and was originally designed to cope with extreme payloads and the rigors of harsh off-highway defense applications. Vastly superior to heavy-duty leaf spring, rubber block walking beam, two-spring “six-rod,” and trailing arm suspensions, the Air Link suspension provides a smooth, comfortable, uncompromising ride.
One of the real benefits of the Air Link suspension is that the ride quality is virtually unchanged when running empty, saving the driver and truck from the pounding associated with steel springs or rubber block suspensions that become too stiff when empty to isolate the driver and equipment from road inputs.
The Air Link is available in capacities ranging from 46,000 to 85,000 lbs and has been adopted in many severe-duty applications. The main reason for fleets trying the Air Link for the first time is to promote driver comfort and equipment protection. Another advantage to the fleet besides driver retention is the potential for more trips to occur in the same shift, because drivers can safely operate unladen vehicles at higher speeds on rough terrain during return trips due to the superior ride characteristics.
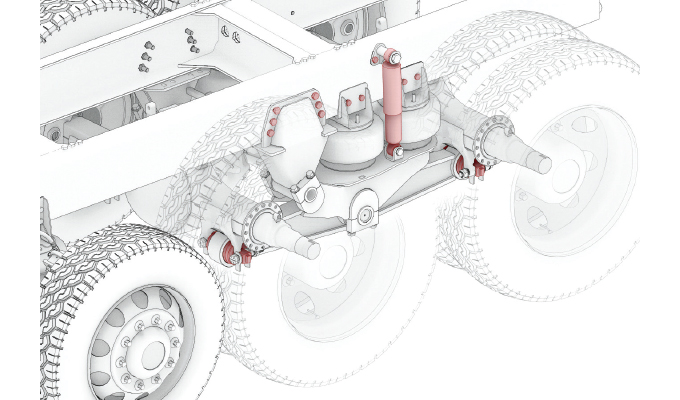
BALANCING ACT
There is no easy suspension solution that addresses all environments and all concerns. While the severe-duty segment of the Class 8 build is small, it is also the most diverse with regard to application, body style, number of axles, ride heights, load center of gravity, and addition of auxiliary axles like pushers, tags, stingers, etc. Here are some factors to consider:
- Truck Load During Use: If your return trips are empty or if your load is depleted as you travel, you should use an air suspension that can adjust the air spring pressure to keep your ride quality, driver comfort, and ride height consistent. The uniform ride height is important to reduce drive line vibration, which is vital to improving the life of the drive line, but also helps reduce vibration inputs the driver may feel.
- 100% Off-highway Use (low center of gravity): If your application spends the majority of time off highway or on poorly-maintained, temporary, worksite roads with lots of articulation events, you should use a walking beam suspension that will offer the best chance of keeping all tires in tractive contact with the ground. If your application has a medium to low center of gravity and zero to two auxiliary suspensions, then I would recommend an air-over-walking-beam for the best driver comfort and equipment protection.
- 100% Off-highway Use (high center of gravity): Similar to above, if your application spends the majority of time off highway or on poorly maintained jobsite temporary roads with lots of articulation events, you should use a walking beam suspension that will offer the best chance of keeping all tires tractive and in contact with the ground. If your application has a high center of gravity and more than two auxiliary suspensions, then I would recommend a spring/rubber type walking beam and would apologize to the driver for the rough ride.
- 25% Off-highway Use: Same as above, but many fleets unwisely use a rubber-ride-walking-beam suspension even though the majority of the time the vehicle stays on maintained roads. However, an air-over-walking-beam suspension would be a better choice for driver comfort, particularly for lower center of gravity applications with limited auxiliary suspensions. I see applications every day that use rubber-ride-walking-beam suspensions that should have used the air option. For example, utility bucket trucks, highway construction equipment, long haul tractors, etc.
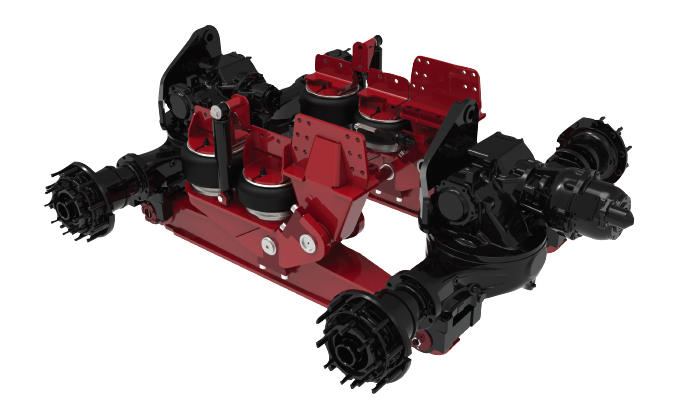
ASK AN EXPERT
If a fleet is specifying a new type of vehicle or configuration that they have not used in the past or want to improve on it, then I would simply suggest they call a qualified suspension manufacturer like Link Manufacturing. This will allow the manufacturer to work through a fleet’s application and point them to the right suspensions—which in some cases might be a competitive offering.
No manufacturer should be interested in selling a suspension into an application that doesn’t suit it well. At Link, we are very aware that there are still a lot of owner operators and small fleets out there and having a power unit out of service can negatively impact their livelihoods. We take our role very seriously.
ABOUT THE AUTHOR
Mark Molitor brings more than 25 years of experience with engineering in the heavy-duty trucking industry to his position as senior product manager, chassis suspensions for Link Manufacturing. Prior to his appointment at Link, Molitor held several roles with SAF-Holland including: vice president product engineering, Americas and vice president product engineering, powered vehicle systems business unit. Find out more about Link Mfg., LTD, and its ROI Cabmate and Air Link suspensions, visit www.linkmfg.com.