For nearly two centuries, humans have designed and built motorized vehicles. The choice of propulsion method was initially driven by practical considerations such as technical feasibility and availability of fuel rather than environmental impact. Although the earliest electric vehicles (EVs) were already locomoting in 1886, the internal combustion engine (ICE) remained dominant for many years. Petrochemical combustion technology is mature and well-established, and recent improvements mainly involve making it more eco-friendly. Efforts such as using alternative fuels, improving exhaust gas recirculation, and implementing hybrid drivetrains and shut-down-on-idle systems have helped reduce emissions, but these advancements are limited in their ability to reach the zero-carbon emissions threshold.
As the transportation industry shifts its focus to EVs, innovation in the field is as brisk and vibrant as any change in technology the world has ever seen. The propulsion, energy storage, and microelectronics components of EVs are experiencing rapid advancements, breakthroughs, and inventions. With this continuous drive toward faster, safer, and more efficient technology, vehicle manufacturers regularly face near-revolutionary engineering decisions.
INNOVATION & ECONOMICS
Bolstered by the Inflation Reduction Act (IRA) and the Infrastructure and Investment Act (IIA), which have dedicated more financial support toward the promotion of zero-emission vehicles than ever before, commercial and specialty vehicle original equipment manufacturers (OEMs) are focused on bringing their all-electric vehicle platforms to market in time to meet growing demand. States like Washington, for example, have moved to ban registration of new ICE vehicles by 2030, leaving OEMs just seven short years to deliver zero-emission commercial fleet vehicles of all types. Furthermore, a growing number have stated their intentions to stop investing in new ICE platforms and models, while many others have already defined a specific date to end ICE vehicle production.
Tax incentives and government commitments to reduce emissions have a visible and direct impact on expanding the North American EV market; however, these bills also present massive but less visible opportunities for economic growth domestically, and US-based manufacturing companies are taking action to benefit from the confluence of market growth and legislation.
With this burst of momentum, EV OEMs and their suppliers now face mounting pressure as they design, validate, and ramp production on an entirely new propulsion system that must meet the range, durability, and reliability required by the commercial vehicle market. Questions about how EV platforms will perform compared to their ICE counterparts remain for many operators, including questions about which technologies best protect and optimize the performance of commercial EV components. Simply scaling up technologies from passenger EVs does not work for these working vehicles.
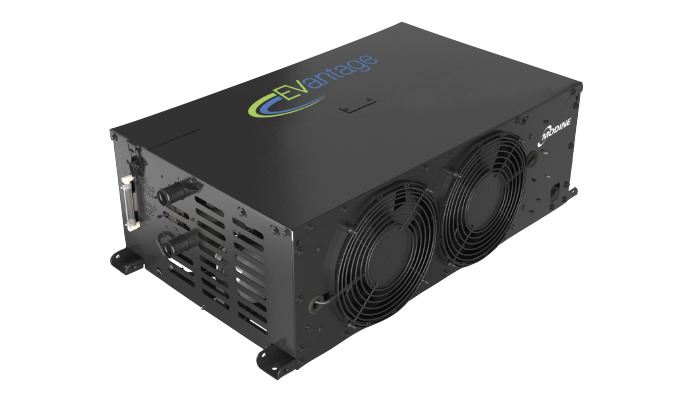
THERMAL FACTORS
The impact of operating temperature on electronic components in EVs is both significant and different from its impact on ICE engines. These vehicles contain numerous power electronics for the inverter, converter and traction motor, and large and complex battery banks. Their longevity, performance, and safety depend on effective thermal management. Designing a thermal management system that efficiently manages thermal loads, fits within the space constraints of a commercial vehicle, and meets heavy-duty operation demands requires specialized knowledge and experience with thermodynamics.
As anyone who has experienced an overheated smartphone or a car engine struggling to start in extreme cold can attest, operating temperature plays a major role in the performance of complex systems. In the case of EVs, electronic components and batteries are not just responsible for starting the vehicle or powering accessories—they are the primary power source. Commercial EVs must be reliable and productive, so the optimal performance of the electronics and batteries is crucial for their success. Extreme heat or cold can severely impact electric powertrain performance, range, and lifespan. Actively managing the temperature of EV components, therefore, is a crucial aspect of EV design.
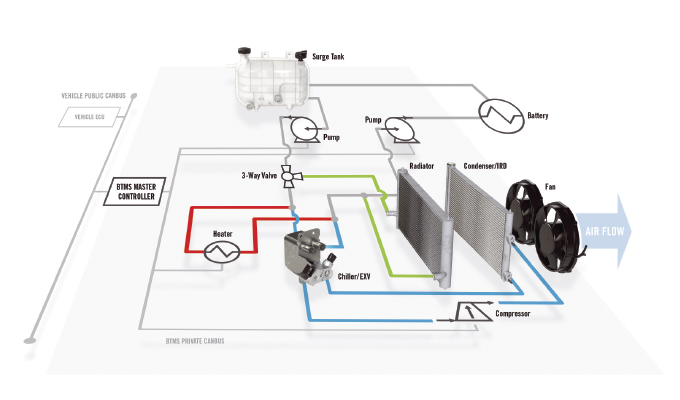
TEMP MANAGEMENT
Thermal management considerations for an EV battery pack include heating and cooling, as the battery is most efficient within a narrow operating temperature window, typically between 77 and 95 degrees Fahrenheit. When the ambient temperature is colder, the Battery Thermal Management System (BTMS) will increase the battery’s temperature. Once the vehicle is in operation, heat generated by the battery pack must be removed to prevent overheating. The switch between cooling and heating, as well as the intensity of each, are managed automatically by the system.
Ambient and operating temperatures similarly affect the various electrical components, such as inverters, converters, traction motors, and related power electronics that charge the batteries. Although these issues have been largely resolved in passenger EVs, commercial, purpose-built, and off-highway EVs face bigger workloads and torque requirements, requiring higher power and battery capacities. This is why commercial EVs are typically equipped with a cooling package for inverters, converters, and traction motors, each with a coolant loop to cool the power electronics, which is then routed through the cooling package to reject the heat to ambient. This circuit keeps the power electronics within the appropriate temperature ranges, ensuring the best performance and the lowest risk of damage to sensitive components.
By regulating temperature and ensuring components operate within their ideal ranges, thermal management improves performance, range, longevity, and speeds up battery charging. Innovations in temperature control for EV propulsion components are crucial for making commercial fleet vehicles viable. Similarly—and perhaps even more so—thermal management will be at the forefront as the industry pivots again from EV technology to fuel cells. So, keep an eye on the thermostat in this space.
ABOUT THE AUTHOR
Gina Bonini is the vice president and general manager of Advanced Thermal Systems at Modine. Find out more, visit www.modine.com.