Cox Automotive Mobility Fleet Services combines industry-leading technology and the industry’s top technicians to deliver fleet maintenance services nationwide. It’s important to the company to ensure its technicians are knowledgeable problem solvers, that’s why it holds a technician competition every year and also sends techs to national competitions, such as TMCSuperTech. Read below to discover the benefits of having top technicians work on your fleet.
WHAT EXACTLY IS TMCSUPERTECH, AND HOW DOES IT DIFFER FROM COX MOBILITY’S OWN TOP TECH EVENT?
COLTRAIN: TMCSuperTech attracts talent from all over North America to compete with the nation’s top professional commercial vehicle technicians. Organized by TMC’s Professional Technician Development Committee, this two-day event features a written challenge and several hands-on skills challenges. This is slightly different from Cox Automotive Mobility Fleet Service’s Top Tech event, which is only open to Cox Automotive Mobility technicians, but also features a technical knowledge and skills competition. Our Top Tech champions and a few top finishers also competed at TMCSuperTech.
WHY DOES COX MOBILITY SEE IT IMPORTANT TO SEND ITS TECHNICIANS TO COMPETITIVE EVENTS? WHAT WOULD IT MEAN TO HAVE A COX MOBILITY TECHNICIAN WIN THE TITLE OF TMCSUPERTECH?
COLTRAIN: At Cox Automotive Mobility Fleet Services, we have 1,000-plus technicians, the majority of whom are mobile. Of this elite group, the top 3% compete in our company’s annual Top Tech competition. These 30 finalists who compete are the most elite of the elite. Of that group, three are named champion each year in the Heavy Duty, Light-Medium Duty, and Trailer categories. Those champions plus a few top finishers will compete at TMCSuperTech. It’s thrilling to see technicians from across the company—top of their game and true masters of their craft—and celebrate their success. I’m rooting for our guys in Cox Automotive Mobility Fleet Services to be top finishers but also wish the best of luck to all the competitors. To have one of our technicians win the title would mean the world. Not just for us in Cox Automotive Mobility, but for them. They work hard, embody the meaning of grit, and are exceptional at what they do. I would love it for them to have that recognized with the prestigious honor of being named champion. In addition, I think it’s fantastic that these elite technicians set such a great example for our younger technicians graduating from FleeTec Academy. They are able to see the kind of opportunities available in a career as a technician, especially for those who are so determined and committed to excellence.
WHAT ROLE DOES A SKILLED TECHNICIAN PLAY WHEN IT COMES TO FLEET MANAGEMENT?
COLTRAIN: At Cox Automotive Mobility Fleet Services, we are driven to “Defy Downtime” for our clients. Downtime is of top concern for fleets operators as it can have rippling effects across the business. Failing to address inefficiencies limits operations and keeps vehicles off the road, hurting profitability. We pride ourselves on being the premier fleet maintenance provider for light, medium-, and heavy-duty trucks and trailers, servicing fleets nationwide. However, we can’t do it without our team of world-class technicians, who play one of the most critical roles in the industry. I truly believe we have the best of the best technicians working for us. They go above and beyond to deliver amazing service day in and day out for our clients. Without them, fleet performance, productivity, and safety would not be possible.
IN YOUR OPINION, WHAT ARE ALL THE NECESSARY COMPONENTS TO HAVING A COMPLETE FLEET MANAGEMENT SYSTEM/STRATEGY?
COLTRAIN: Having skilled technicians is certainly at the top of the list. They are the lifeblood of our business and true partners to our clients. Overall, I’d say the key element of a successful fleet maintenance management program is a quality preventive maintenance program. The saying, “An ounce of prevention is worth more than a pound of cure,” comes to mind. Quality preventive maintenance starts with highly trained and skilled technicians who can identify and repair issues before they become catastrophic failures that lead to fleet downtime.
Of course, this also includes up-to-date telematics and expert fleet managers. I’d also add top-notch training to the list. We are proud to offer FleeTec Academy, our intensive, hands-on residence training program. There, we teach truck maintenance and repair skills from the ground up. Our FleeTec graduates have seen great success with the program, and a few even competed at our company’s TopTech competition. We also offer advanced training for our more established techs. To round out the list, a culture of safety is critical.
WHAT IS ONE THING YOU WOULD LIKE TO SHARE WITH OUR READERS CONCERNING THE IMPORTANCE OF HIRING SKILLED TECHNICIANS?
COLTRAIN: Technicians are the backbone that keeps America moving. Without them, fleet operations would not be possible. Hiring and training technicians to be up to par with industry standards is key to success, not only for fleets but also for our nation’s supply chain and the consumer.
As fleet managers and operators in the industry, we rely on service technicians to keep vehicles up and running. Now it’s time to spotlight technicians. Modern WorkTruck Solutions chatted with two Cox Mobility technicians about their experience at TMCSuperTech and more.
WHAT WOULD IT MEAN TO YOU TO PLACE FIRST IN AN EVENT SUCH AS THIS?
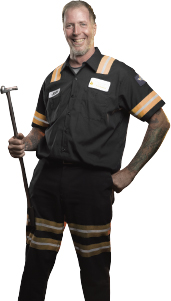
LAWHORN: I’d probably cry. But there are a lot of smart people in the competition. I don’t know the guys I’m competing against, so there might be a chance. We are competing against each other, but we are all rooting for each other. We are excited for each other. But winning, I don’t really care about that. I didn’t have to overcome anything; I’ve just been good at it. I didn’t just take some magic potion—I just happen to be good at taking tests.
kerfoot: It would be amazing. It means that I did my best and that I did it better than the other guys. It would be great to take first again. I won in 2018. To show that I’m still top of my game and that I’m this year’s current champion, it’d be nice.
IN YOUR EXPERIENCE, HOW MUCH DEDICATION/TRAINING DOES IT TAKE TO BE A TOPTECH FOR COX MOBILITY?—OR IS IT ALL PURE SKILL?
LAWHORN: I didn’t do any extra training. I happen to know what I know, which is mechanics. I’ve been turning wrenches since I could hold them. I’m not afraid to be wrong; I’ve learned a lot from really smart people. I’m always training to be better, not necessarily for the next competition. I was a helicopter tech in the Marine Corps, where I received the title class honor man. I can’t explain how to absorb information—we all learn differently. I learn hands on. You can tell me, but it won’t sink in. Some people don’t know how to learn. I build hot rods in my spare time to see if I can do it. I don’t fix my own stuff, but I love fixing other people’s trucks. I enjoy knowing that my efforts make someone’s life easier or better. Whether it’s being a mechanic or a friend, if it’s valuable to someone else I’ll put forth the effort. I put people ahead of myself.
KERFOOT: Honestly, I just show up and compete. The first year I ever competed, Cox’s FleeTec Academy instructor, Dave Grubb, came by the shop and asked if I was studying; I said no. He gave me some grief. Then I placed fourth overall, and he hasn’t given me grief ever since. I haven’t studied for any of this. I just go off of what I know. I take any training course I can get into. You’re always learning as a technician—there’s always a different procedure. This isn’t one of those careers where you get out of school and you don’t have to learn again. I go to training at OEMs and periodically dealerships would offer different trainings. Meritor would give brakes classes. It’s pretty much all in-person training.
WHAT DO YOU FEEL IS YOUR ROLE IN A COMPLETE FLEET MANAGEMENT SYSTEM AS A SKILLED TECHNICIAN?
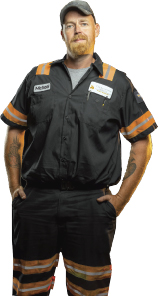
LAWHORN: Fix trucks, get the customer back up and running, and get the customer taken care of so they can get going. I’m not as much in the business of fixing trucks as I am finding solutions. Maybe it’s something I can fix, maybe the equipment is too worn out to repair. To me it’s fixing trucks and being there when the customer needs me to be there.
KERFOOT: To keep the fleets’ equipment up to par and reduce breakdowns and maintenance costs. If we can find something before it breaks, before it becomes an issue, it’s a lot cheaper to repair than after it breaks completely. If we find it during a standard inspection, I ask, “When can we schedule this for repair?” That reduces their long-term downtime and total cost of ownership. It’s just like a roof on a house—you need to catch the leak before it starts causing real damage. If you repair it too long after the leak happens, you’ve got to repair the roof and all the water damage it causes. I had a customer that lost brakes on their vehicle because their brake pads were grinding for so long it destroyed the caliper. So, they had to replace the caliper, the pads, and the rotor. Whereas if that was caught during a maintenance inspection, I would have said, “Hey, your pads are low, let’s get those replaced,” and that would have saved them from paying three times the cost of repairing all of the other damaged parts, including the busted caliper.
OUR READERS ARE FLEET OWNER/OPERATORS. WHAT WOULD YOU LIKE TO SAY TO THEM AS FAR AS WAYS THEY CAN SUPPORT YOU WHEN YOU’RE PERFORMING MAINTENANCE ON THEIR VEHICLES?
LAWHORN: Enforce accountability on how drivers are taking care of their equipment. Implement RP (recommended practices) on quality pre-trip and post-trip inspection. That’s the single best controllable way to optimize your fleets’ performance. Drivers spend the most time in the truck, they know what’s going on.
KERFOOT: Give us the time to do the job. Don’t schedule it last minute, and don’t tell us we have one hour to do a three-hour job. Give us the time to do it properly. In the long term, that’s going to be the best solution for your vehicle and your business and reduce out-of-service violations on your equipment.
FOR MORE INFORMATION
Ted Coltrain is the vice president of operations at Cox Mobility. Josh Lawhorn and Michael Kerfoot are both senior mobile diesel technicians at Cox Mobility. Find out more, visit www.coxautoinc.com.