By Spencer Martineau and Kevin Griffith
Tightening emissions standards around the world have driven diesel engine manufacturers to develop technology that can enhance fuel economy while dramatically reducing emissions. To those ends, many truck makers have deployed new methods to maximize efficiency as well as a variety of exhaust aftertreatment devices to mitigate nitrogen oxides (NOx) and particulate matter (PM) that contribute to air pollution.
However, servicing and maintaining new model equipment can become something of a headache for fleet owners. If service lapses, repair or replacement of certain equipment or componentry can become costly and unexpected when your dashboard lights up with fault codes.
Protecting your bottom line means protecting your fleet. Here are some considerations to take and how to maximize the life of more sophisticated newer model trucks anywhere.
MAXIMIZING DPF LIFE
One of the most common aftertreatment devices introduced over the past decade is the diesel particulate filter (DPF), which has become standard on many newer diesel-powered vehicles. These devices have been shown to trap and oxidize up to 100% of carbon soot particulates in the engine exhaust and as such, have proven effective at meeting the evolving emissions targets in recent years.
DPFs are commonly installed behind the truck cab and are similar in size and shape to a conventional truck muffler. Warranties for DPFs typically run for about 500,000 miles. Fleet owners can visually identify when the filter element has reached the end of its life when holes or cracks appear that allow unfiltered exhaust to flow downstream.
Throughout its lifetime, the DPF should typically be removed and cleaned two or three times to remove accumulated ash. The range of DPF service intervals, according to diesel engine builders, is between 80,000 miles (in severe service) and 250,000 miles (under ideal conditions). The typical long-haul heavy-duty diesel truck travels more than 100,000 miles per year, so depending on the severity of the duty cycle, off-truck cleaning of the DPF should take place between once a year and once every three years. Maintaining an appropriate service schedule is important—if a replacement is required, it can cost an average of $3,000 or more.
Importantly, the DPF can become blocked with ash and rendered ineffective far more quickly if a lubricating engine oil with high Sulphated Ash Phosphorus and Sulphur (SAPS) content is used. Choosing an engine oil with low SAPS will reduce DPF blockage ensuring cleaner exhaust gas, maintaining vehicle efficiency and less maintenance. Further, deposit control additives can help reduce soot loading, therefore helping to reduce the likelihood of DPF blockage.
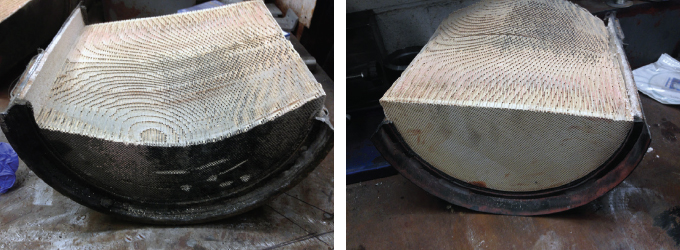
FUEL INJECTOR DEPOSITS
In an ongoing effort to maximize fuel economy, modern diesel engines may run faster and hotter than ever before.
The most advanced also bring in multiple fuel injection events in every engine cycle. Here, very rapid movement of very low momentum parts is required to generate the necessary energy—and those parts are more prone to sticking. While these conditions are good for maximizing engine efficiency and emissions, they can potentially lead to operational problems if the right measures are not taken. In the past, engines like the Cummins L10 might have tolerated internal diesel injector deposits. These new conditions make it more likely for problems to occur.
Hotter engine temperatures and multiple fuel injection events can also lead to new types of fuel injector deposit formations, specifically both nozzle coking and internal diesel injector deposits (or IDIDs) that can be found in high-pressure common-rail (HPCR) fuel injection systems. IDIDs can cause sluggish movement of fuel injector parts, or even sticking, interfering with fuel being injected into the combustion chamber. All these kinds of deposit formations will ultimately lead to inefficient combustion cycles—leading to lost fuel economy, increased emissions, soot loading of DPFs, and in the worst-case scenario, preventable downtime while service takes place.
Deposit formations on fuel injector systems can create these unforeseen challenges for fleets of all sizes. Replacement costs typically run about $400 or more per injector. What’s more, many fleet operators who have invested in modern equipment generally expect that the fuel efficiency benefits will eventually outweigh the investment cost. Unexpected repair or replacement costs can be a major blow to the bottom line.
DIESEL ADDITIVES
Luckily, there is an effective and economical means to minimize deposit formation on fuel injectors, as well as reduce excessive soot loading of DPFs. Fleets can use a diesel fuel additive that contains Deposit Control Additives (DCAs), which effectively remove deposits and allow for more efficient combustion cycles that reduce soot loading, increase fuel economy, improve emissions, and increase uptime.
In an effort to best protect fuel systems, fleet owners should note that seasonal preparation will play an increasingly critical role as fuel supplies change with respect to new regulations. For example, diesel fuels are more susceptible to gelling in cooler temperatures, which can lead to unwanted downtime and significant loss in revenue for fleets and consumers while their vehicles are repaired. While fuel systems have improved over time to prevent this kind of issue, fuel filters and decreased filter pore sizes have made modern systems more cold-temperature sensitive than ever before. All of this makes proper cold-flow additives an essential consideration for vehicles using biodiesel in order to prevent fuel filters from plugging and shutting down all fuel flow.
Purchasing these kinds of diesel fuel additives represents a minimal investment to protect fleets in comparison to thawing and towing costs—which run a fleet operator up to $4,000, not including the additional expenses of downtime, undelivered goods, driver expenses, and vehicle repairs.
MODERN ENGINES & FLUIDS
Engine technology is changing—and that means engine lubricants and fuels must change with them.
Work with your fluids supplier to ensure that your fleet is serviced with the proper fluid technology. The right fuels and fluids can help newer model vehicles move cleaner and achieve optimal performance, as well as prevent unforeseen maintenance issues that can cost you money.
ABOUT THE AUTHORS
Spencer Martineau is a diesel additive product manager at Lubrizol. Kevin Griffith is a fuel additive product manager at Lubrizol. Find out more, visit www.lubrizol.com.